
- Created2017.05.25
KIMM Advances Mass Production of Next-generation Display
-KIMM developed micro-LED display manufacturing technology usingaroll transfer process for the first time in Korea
-Reduced power consumption by 1/2, Increasedproduction speed by10,000 times, Technology transferredto 6 companies
- Outcome report ceremony held on July 20 for ‘Development of infrastructure for flexible devices with high performance using nanomaterials’ project
“This next-generation display changes its shape freely. Although it boasts high resolution, its power consumption is only half that of an OLED display and the production speed is 10,000 times faster.” The key to the display of everyone’s dreams is the possibility of mass production. With the micro-LED display manufacturing technology developed by the Korea Institute of Machinery & Materials (KIMM, President Dr. Park, Chun-hong), all of this is realized, as power consumption and production speed are improved dramatically.
Using a roll transfer process* , the Department of Applied Nano 2 Mechanics (Head, Dr. Kim, Jae-Hyun) at KIMM developed a production technology for micro-LED display** with low power consumption and high mechanical reliability and flexibility. Luminous efficiency is 3 times better than those of LCD and OLED displays, and production speed is 10,000 times faster than was conventionally achievable.
* Roll transfer process: The process of picking up the micro- and nano-elements on a temporary substrate with a roll stamp and then placing the elements on a desired substrate.
** Micro-LED display: Light Emitting Diode. Micro-LEDs made of monocrystalline inorganic materials are placed in each pixel to improve the reaction speed and luminous efficiency.
KIMM holds the original patents for the roll transfer process and succeeded in the first development and technology transfer in Korea. In the first step of the roll transfer process, a roll stamp picks up an array of TFT*** elements, which serve as a switch for each pixel of the display, and places these elements on a temporary substrate. In the second step, the array of LED elements is lifted off from a semiconductor wafer and placed on 3 the substrate on which the array of TFT elements is disposed. Finally, an active matrix**** type micro-LED display, with a structure in which the two elements are interconnected, is transferred onto a target substrate.
*** TFT (Thin Film Transistor): A semiconductor device for constituting an active matrix type display, which functions to turn on / off each pixel of a display.
**** Active matrix: A control method capable of actively controlling each pixel of a display, which has advantages in that the display response speed and power efficiency are significantly increased as compared with a passive matrix.
The micro-LED, composed of single crystalline inorganic material used in this technology, has 3 times higher luminous efficiency than OLED and has low power consumption and excellent durability, making it suitable for mobile and wearable displays. In addition, since there is no restriction on the substrate, it can be transferred onto a stretchable and transparent rubber substrate. Therefore, it is expected to be possible to manufacture a transparent display which can freely change its shape
KIMM’s research team developed the TFT device fabrication technology using the roll transfer process together with professor Ahn Jong-hyun's research team from Yonsei University in 2012. The two groups developed multi-transfer technology enabling the alignment of TFT and LED devices sequentially. This result was published as an article in the journal of Advanced Functional Materials in 2017 (DOI: 10.1002/adfm.201606005) Furthermore, reflecting the demand from the industry, KIMM’s team has also secured the original process technology that uses the metal alloy in order to transfer the micro-LED device to the substrate and realize the electrical connection simultaneously. By virtue of this process, the production time and cost is significantly reduced.
Because of the shortened production processes, the production speed has been dramatically improved. While die bonder**** equipment, widely used in production for conventional LED displays, can mount 1 ~ 10 LEDs per second on the board, the current roll transfer equipment can transfer more than 10,000 LEDs per second. 5 It takes more than 30 days to produce a full-HD 2-megapixel 100- inch digital signage by the die bonder process, but the roll transfer process can be done in less than an hour and the process cost is incomparably low.
***** Die Bonder: The term "die" refers to a chip. When manufacturing a transistor or an IC, die bond or bonding is the process to attach the chip to a stem or lead frame. This machine is called a die bonder.
Roll transfer technology also allows flexible, stretchable, and lightweight displays because the technology is capable of transferring micro-LEDs of less than 100 micrometers in size and thin-film LED devices of less than 10 micrometers in thickness. The existing die bonder equipment is unable to effectively deal with micro-LEDs.
The research team created this achievement through the “Development of infrastructure for flexible devices with high performance using nanomaterials” project supported by the Ministry 6 of Science, ICT, and Future Planning. An outcome report ceremony was held on Thursday, July 20 at The K Hotel in Seoul. The ceremony was attended by numerous guests including officials from the Ministry of Science, ICT, and Future Planning, operators from six enterprises that KIMM transferred the roll transfer technology, and entrepreneurs seeking technology transfer consultation.
KIMM signed six technology transfer contracts through this project with six companies. Lumens Co., Ltd., a medium-sized display company, received the digital signage manufacturing equipment and manufacturing process technology based on LED roll transfer technology from KIMM. If Lumens builds mass production lines for micro-LED displays in the future, Korea will not only secure global leadership in the field of micro-LED displays, but also contribute to the creation of a domestic industrial ecosystem including small and medium-sized enterprises. KIMM also agreed to an MOU with Lumens for more technical cooperation.
KIMM transferred thin film roll transfer equipment technology to IES 7 Co., silicon device roll transfer equipment technology to Flexcom Co., and film material technology for the transfer process to RPE Co., respectively. In addition to establishing a foundation for the manufacture, evaluation, and application of high-performance flexible devices for joint use among industry-academy-research institutes through this project, KIMM has established a mass production foundation for high-performance flexible displays, high-efficiency flexible solar cells, and single crystal silicon flexible memory. In addition, through this project, KIMM has published about 60 domestic and international papers and obtained about 80 patents.
Dr. Park, Chun-hong, President of KIMM, said, "In the era of the Fourth Industrial Revolution, in which the distribution of information will greatly increase with the development of advanced technologies such as AI (artificial intelligence) and IoT (Internet of Things), new display technologies are required such as rapid displays that transmit a large amount of information in real time, adaptive flexible displays that can be changed on demand, and flexible transparent 8 displays for ultra-high-resolution ARs (augmented reality) with low power consumption. In cooperation with industry, academia, and research institutes based on the original technology of roll transfer, we will lead the global market of high-performance flexible device manufacturing equipment.”
Attachments:
- Attachment 1: Roll-based multiple transfer technology schematic diagram
- Attachment 2: The researchers at Department of Applied Nano Mechanics of KIMM andMicro LED production site (photo)
- Attachment 3: Back cover paper published in Advanced Functional Materials, March 2017 (cover and paper image)
- Attachment 4: Outcome report ceremony for “Development of infrastructure for flexible devices with high performance using nanomaterials” project (photo)
- Attachment 5: MOU agreement of KIMM-LUMEMS (photo)
- Attachment 1: Roll-based multiple transfer technology schematic diagram
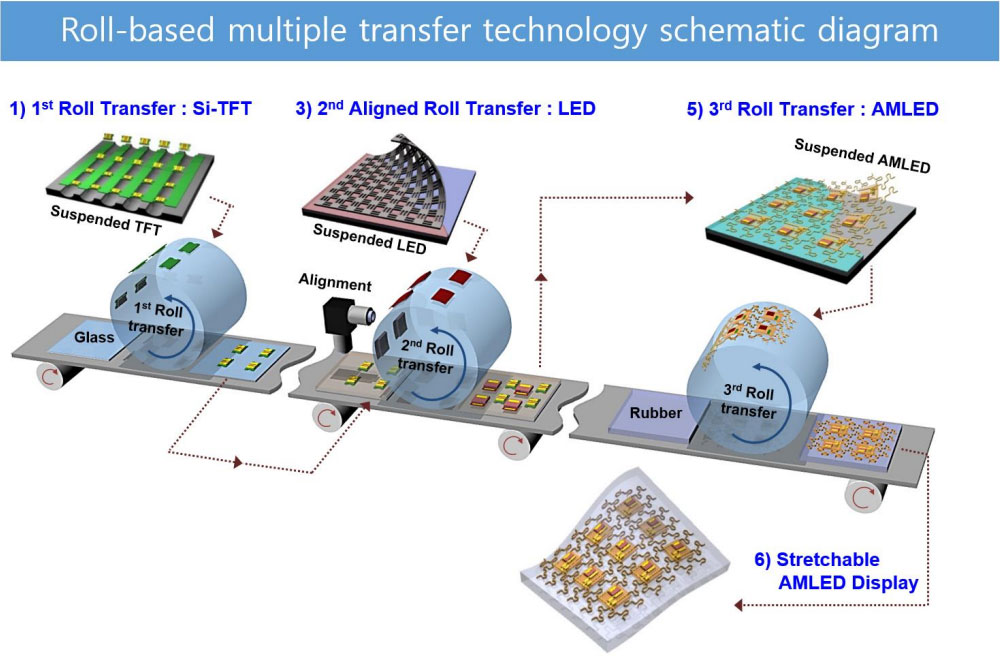
- Attachment 2:Theresearchers at Department of Applied Nano Mechanicsof KIMM andMicro LED production site (photo)
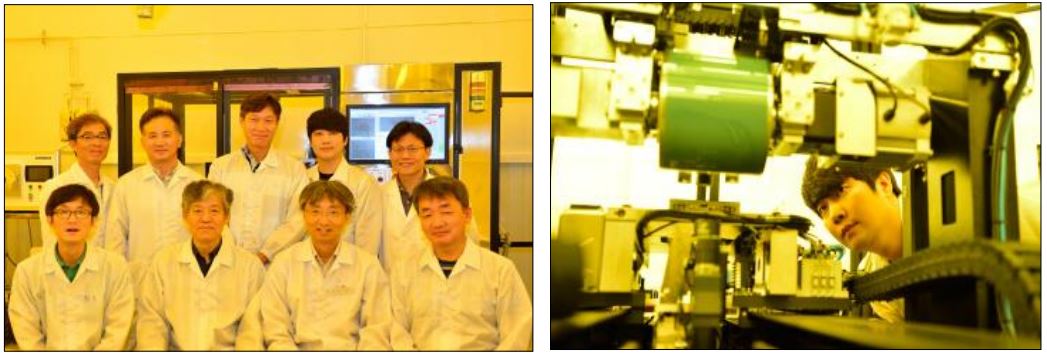
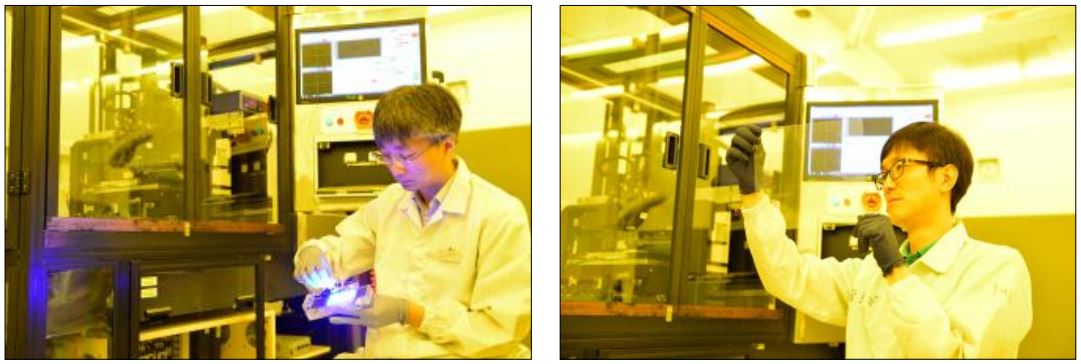
- Attachment 3:Back cover paper published in Advanced Functional Materials, March 2017 (cover and paper image)
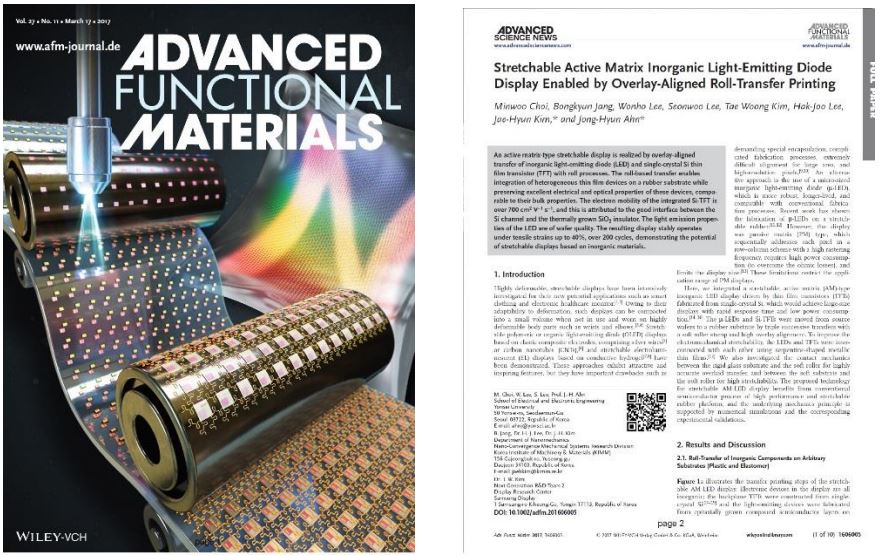
- Attachment 4:Outcome report ceremonyfor “Development of infrastructure for flexible devices with highperformance using nanomaterials”project (photo)
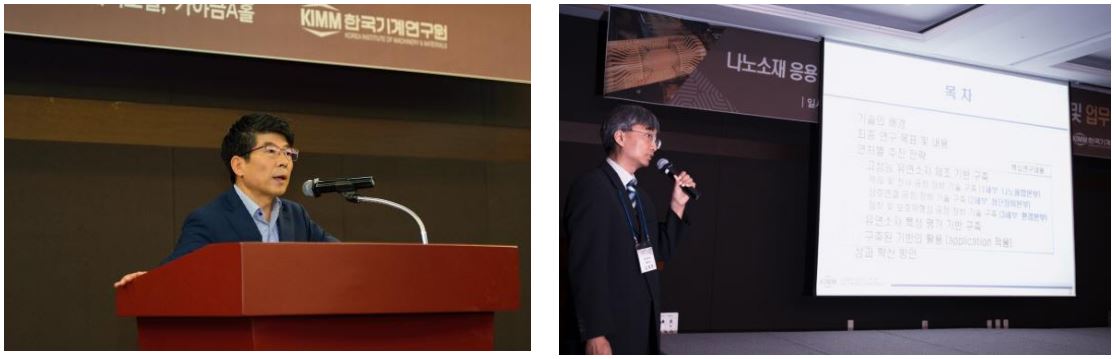
- Attachment 5:MOU agreement of KIMM-LUMEMS (photo)
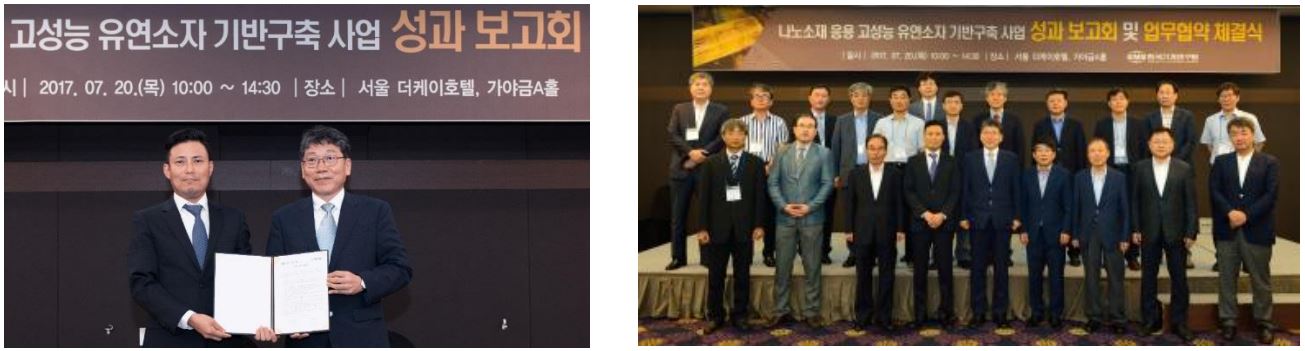