Magnetic bearing technology using the principle of magnetic
levitation for the rotor to rotate in the state of complete levitation
to enable high-speed rotation at 100,000 rpm or faster and highprecision
rotation with rotating vibration below 2 μm
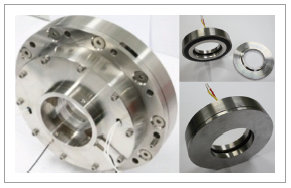
Client / Market
- Magnetic bearing manufacturer
- Turbo machine (compressor, blower, turbine, pump) company
- High-speed spindle company, ultracentrifuge company
- Precision roller (for printed electronics, nano imprint) manufacturer and application
company
Necessity of this Technology
- Existing ball bearing has limits regarding high-speed and precision of rotary machine.
- When applying ball bearing for a rotor with a diameter of 50 mm, rotation at up to
30,000 rpm can be achieved.
- In the case of a low-speed precision roller where ball bearing is applied, rotating
vibration of 20 to 40 μm occurs.
- To develop a high-speed, high-precision rotary machine with rotating speed
over 100,000 rpm and rotating vibration of 2 μm, a magnetic bearing that enables
contactless rotation in the state of complete levitation needs to be applied.
Technical Differentiation
- Energy efficient magnetic bearing using a permanent magnet and electromagnet
- Homopolar structure to eliminate the high heating issue of heteropolar magnetic bearing
- The volume of entire system reduced by integrating the auxiliary bearing and
sensors with magnetic bearing and achieving a shorter length for magnetic bearing
- With a short length for rotor, the primary bending mode frequency can be increased
for enhancement of rotation stability at high speed.
- Minimization of usage of the electric current and rotational vibration by applying
self-weight compensation and permanent magnet for bias force
- Lubricant is not required because it is contactless and frictionless, and clean
bearing of which life time is semi-permanent
- Smart bearing with real-time vibration/load monitoring to cope with dangerous situations
Excellence of Technology
- Applied for an ultra-high-speed spindle with rotor with a diameter of 41 mm and
achieved rotation speed of 120,000 rpm and linear velocity of 49.2 Mil-DN
- Applied for a low-speed high-precision roller and achieved rotation speed of 30 rpm,
and rotating vibration below 2 μm under the condition of 300 N load
- External vibration and load is monitored real-time to detect abnormality in system
in advance.
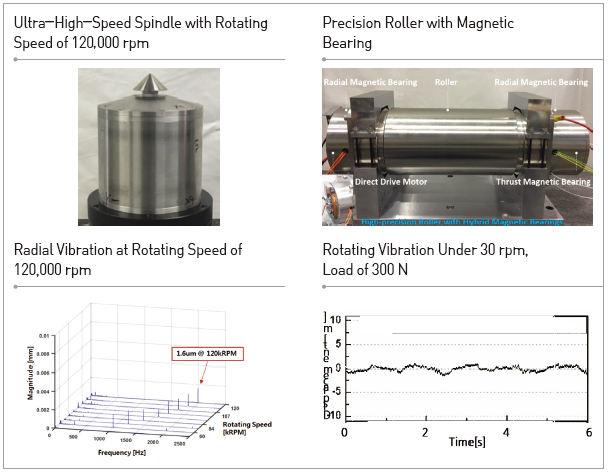
Current Intellectual Property Right Status
PATENT
- Turbo Machine Equipped with Magnetic Bearing (KR1287057)
- Magnetic Bearing Using Permanent Magnet and Electromagnet (KR0976631)
- Magnetic Bearing System (KR1133560)
- Magnetic Bearing Structure and Turbo Machine Equipped with this Magnetic
Bearing (KR1166854, US9041266, SE536808, CNZL201180013360.X)
- Composite Magnetic Bearing Having Auxiliary Bearing Coupled Thereto (KR1408060,
US9273723, CNZL201380006733.X)
- Composite Magnetic Bearing Having Sensor and Auxiliary Bearing Coupled
(KR1444139)
- Thrust Magnetic Bearing for Deflecting Force Compensation (KR1552350, US14/674022,
CN201510196685.6)
- Roller Module Equipped with Magnetic Bearing and Permanent Magnet (KR1809104,
US15/554729, UK1708962.4)
KNOW-HOW
- Ultra-high-speed rotor design, manufacturing technology
- Ultra-high-speed, high-precision magnetic bearing control technology
- Inductive displacement sensor technology
- Real-time vibration, load monitoring and emergency situation handling technology
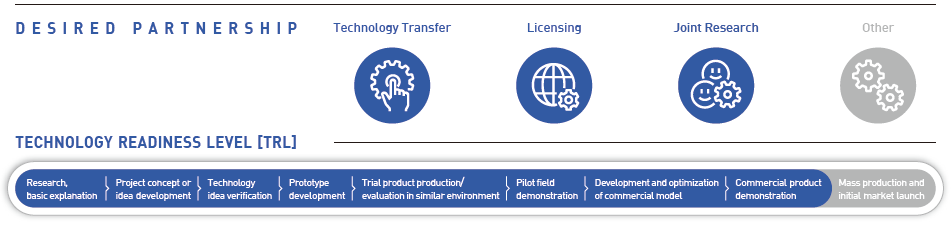
|